Hydrovolt's recommendation for design to recycle
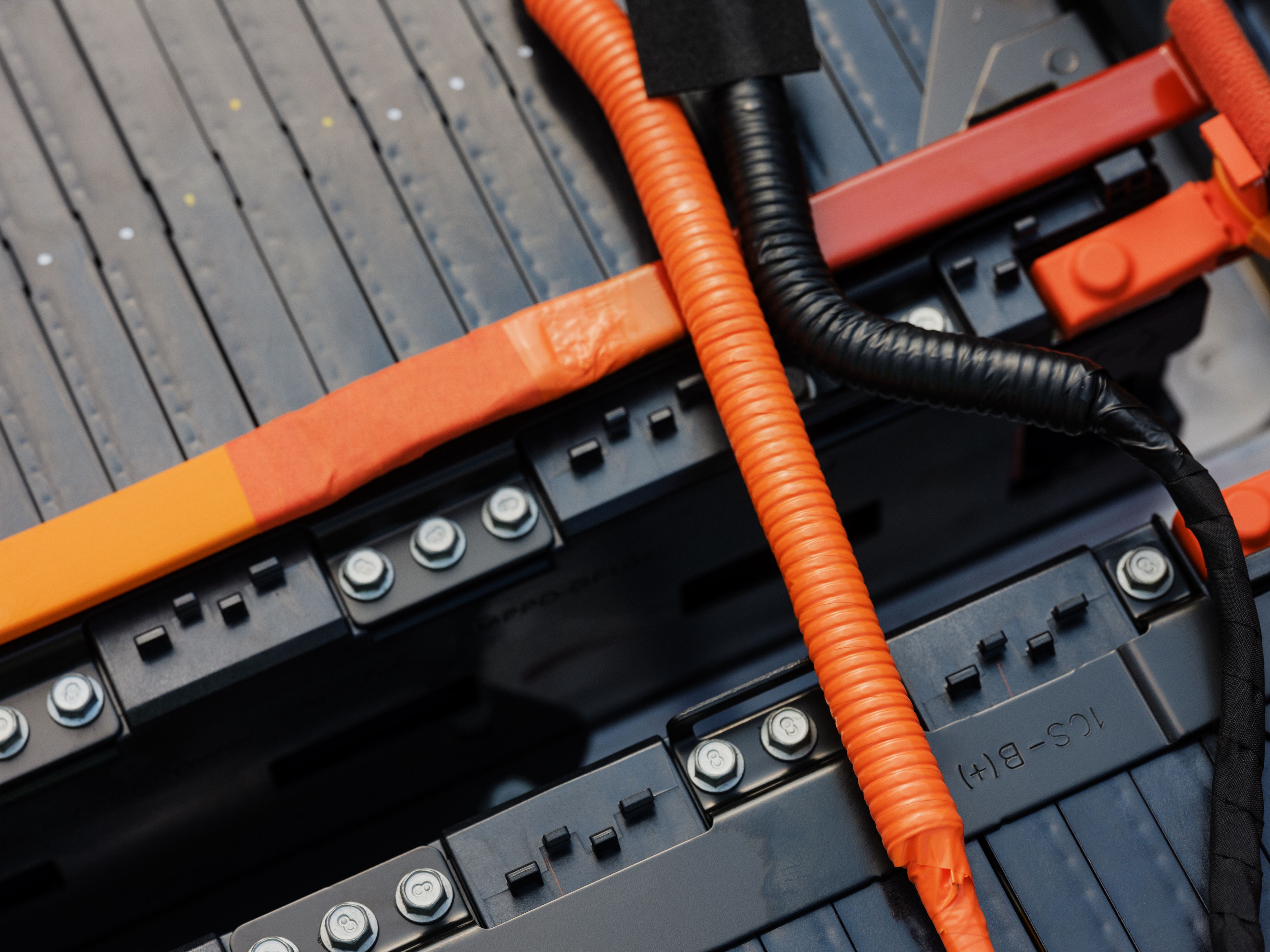
Lets look at how you can become fit for recycling. Below is Hydrovolt’s recommended approach for the design to recycle batteries.
Make us feel electric
In today’s battery market, no industry standard exists for designing and producing battery modules and packs. The result is a variety of designs, which makes it challenging to implement efficient and automated recycling processes.
This is particularly true for the discharging and dismantling processes of batteries needed to maximize recycling efficiency and recovery rates. After these steps, the modules can enter a unique, dry crushing process designed to maximize recovery rates and quality of output fractions.
To maximize the recycling efficiency rate and the recovery rates of critical raw materials, design for recycling will be key to obtain efficient, safe, and sustainable recycling processes.
Our three-step recommendation for efficient battery recycling
Step 1 – help us discharge safely!
- Access: We need as much information as we can on each battery pack to ensure the safest storage on site until preparation for discharge.
- Access: We need access to the battery management system (BMS) to perform a diagnosis and safe discharging without opening the battery.
- Access: Leave us with an accessible hatch in the transport boxes for performing the diagnosis without completely unpacking each.
- Access: If we need to open the battery before discharging, ensure there is good access to connection points in the high voltage circuit.
Step 2 – help us dismantle faster!
- Less: Align type of screws and do not leave us with too many as we want to be enabled to work faster and easier.
- Less: Avoid nasty glue and welding of covers to get rid of cutting to open batteries – and to help us work in a safe manner. Cutting emits harmful fumes.
- More: Design the battery pack in a way that lets us dismantle as many fractions from modules and cells as possible before they enter crushing and sorting.
- More: Make it easy to separate the various materials such as electronics, plastics, etc. to help us sort and recycle all parts of the battery, as we want to become truly circular.
- More: Design your packs to let us easily stack them on top of each other, it makes storing and transport much smoother.
- More: Think about design for easy lifting of both battery packs and modules to make this part safer and more efficient.
Step 3 – help us maximize the value of the critical raw materials!
- Less: Avoid all the sticky and soft materials such as glue, thermal paste, residues of coolant, etc., as it contaminates the recycled materials and leaves us with lower recovery rates and poor quality of the outputs.
- More: We want as much data as possible on the content of cells, including details on organic materials like electrolytes, binders, and more, to avoid any surprises in the crusher.
- More: Design your battery packs in a way that makes it easy to divide the pack into modules – it will make our crusher smile. Cell-to-pack design is particularly challenging.