Pioneering battery recycling for a better planet
The megatrend of electrification is transforming industries and daily life, driving a surge in demand for batteries and critical raw materials. As more sectors—from transportation to energy storage—shift to electric power, the need for efficient, high-capacity batteries skyrockets.
Electric vehicles (EVs) and renewable energy solutions rely on advanced, industrial batteries, making them the backbone of a sustainable future. This transition requires vast quantities of critical raw materials like lithium, nickel, and cobalt, fueling an unprecedented demand as electrification reshapes our world into a cleaner, greener, and more connected place.
The current battery value chain, from production to refining, is dominated by one to a few countries and the critical raw materials from batteries are often mined in conflict-affected areas, raising ethical concerns and creating supply chain vulnerabilities. Particularly for Europe, with high sustainability ambitions and limited access to critical raw materials due to geography.
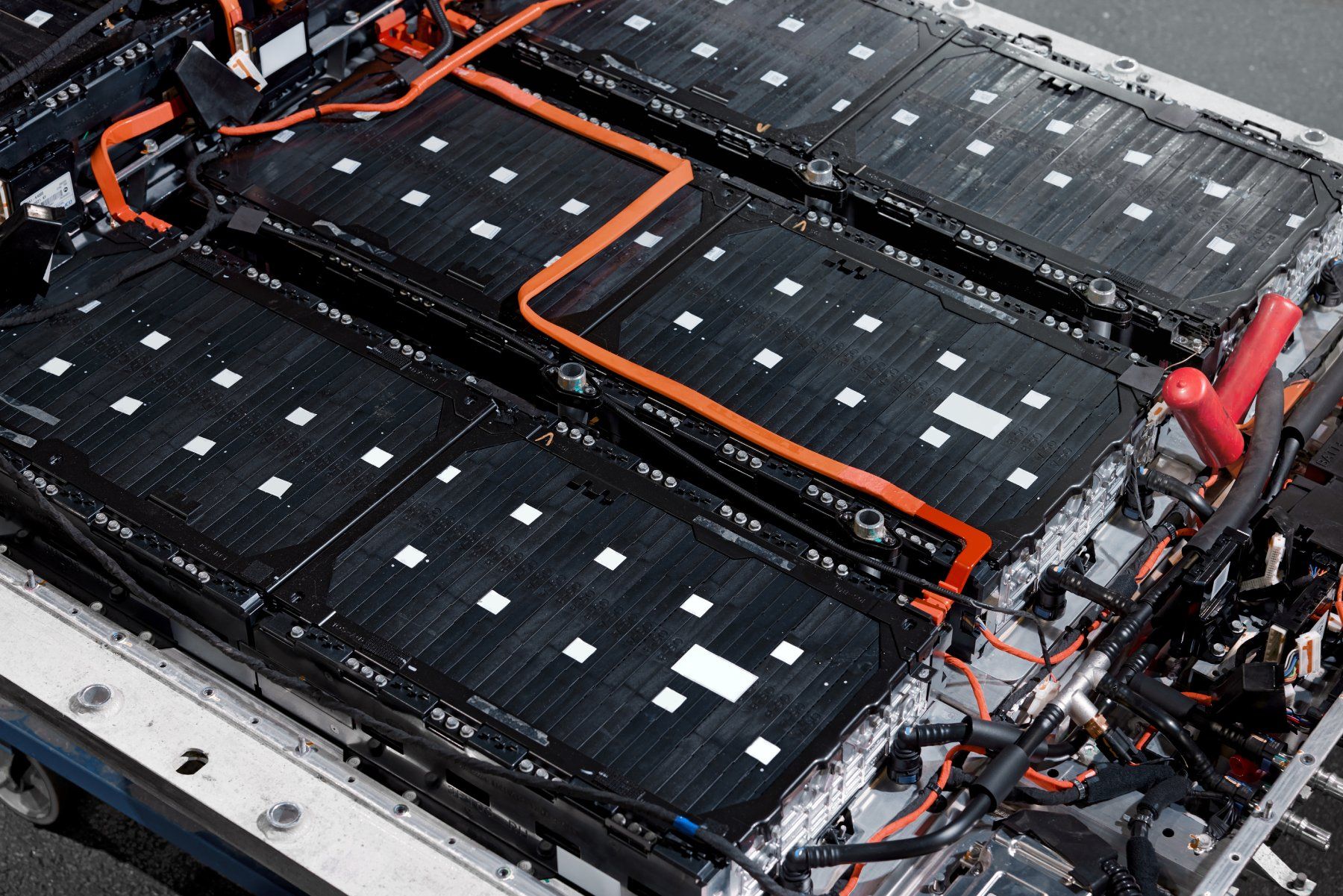
We work to solve three challenges
Reduce waste and manage waste in a sustainable manner
Increase access to critical raw materials through the supply of sustainable secondary raw materials
Reduce emissions for new products and minimize our impact on nature
To address these challenges, and to help reach our climate targets and provide materials needed in the energy transition, the need for sustainable alternatives has become urgent. When batteries reach end-of-life, they can potentially be a large waste issue, and the production of batteries can have a large carbon footprint and impact on nature.
Through battery recycling solutions, a battery can become a battery an infinite number of times. By recycling the materials in the battery, we can create the same high quality as a new battery, replaced with secondary raw materials.
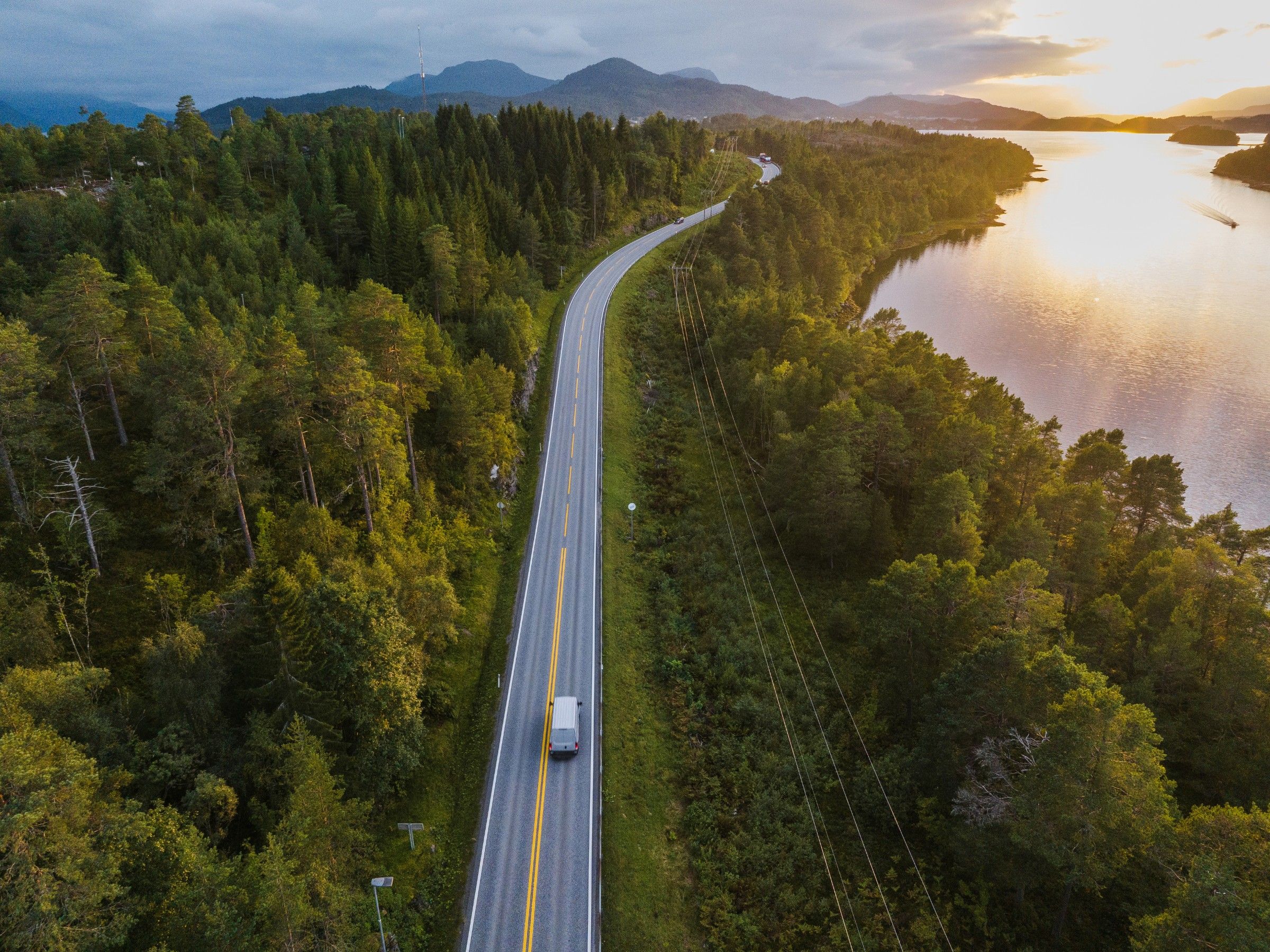
By recovering the critical raw materials from used batteries, recycling reduces reliance on conflict minerals, minimizes environmental impact, and diversifies supply sources, paving the way for a more ethical and resilient battery industry.
Together, we can create a circular battery value chain through urban mining, local recycling capacity and a sustainable approach to making new batteries.
That’s why we work to solve three challenges through our efforts in Hydrovolt.
Our technology for recycling EV – and industrial batteries allows for production of high-quality secondary raw materials while maintaining a high degree of safety throughout the process.
We want to do it right from start. That’s why we strive to think circular in all parts of our processes and ways of working.
Accelerating the transition to a circular world
Our products are one of the best in the market, delivering recovery rates above 90% and the first low-carbon black mass in the industry. Our recycling efficiency rate is something we are proud of and continuously work to improve.
That’s why our operations run on renewable energy, solar power systems, and battery energy storage systems. The recovered residual energy from our collected batteries is used for our own energy needs or to supply the power grid when needed.
Our products are one of the best in the market, delivering recovery rates above 90 percent and the first low-carbon black mass in the industry. Our recycling efficiency rate is something we are proud of and continuously work to improve.
At Hydrovolt, we want to bring back 100% of the materials to make a truly circular battery value chain.
Of course, this would never be possible without our people. We strive to develop a strong and inclusive organization, in which always sets safety as its top priority.
Leading the way in the industry is paramount for us to succeed with sustainable battery recycling. And through that, we promise to ensure that no battery is ever wasted.
Carbon footprint of extracting critical battery materials by conventional mining vs. producing critical battery materials by recycling
A life cycle assessment has been carried out to calculate the carbon footprint of our operations. Using a cradle-to-gate approach, where the cradle is defined at the beginning of the collection process and the gate defined after the C&S process, before the black mass is sold to offtakers.
The result concludes on a very low carbon footprint of less than 0,2 kg CO2 per kg black mass, proving it is possible to develop greener batteries through recycling and the use of secondary raw materials in new batteries.
With lower environmental footprint, recycling is a more sustainable alternative to conventional mining. The assessment shows that we have a 75 percent lower carbon footprint compared to extracting materials by conventional mining.
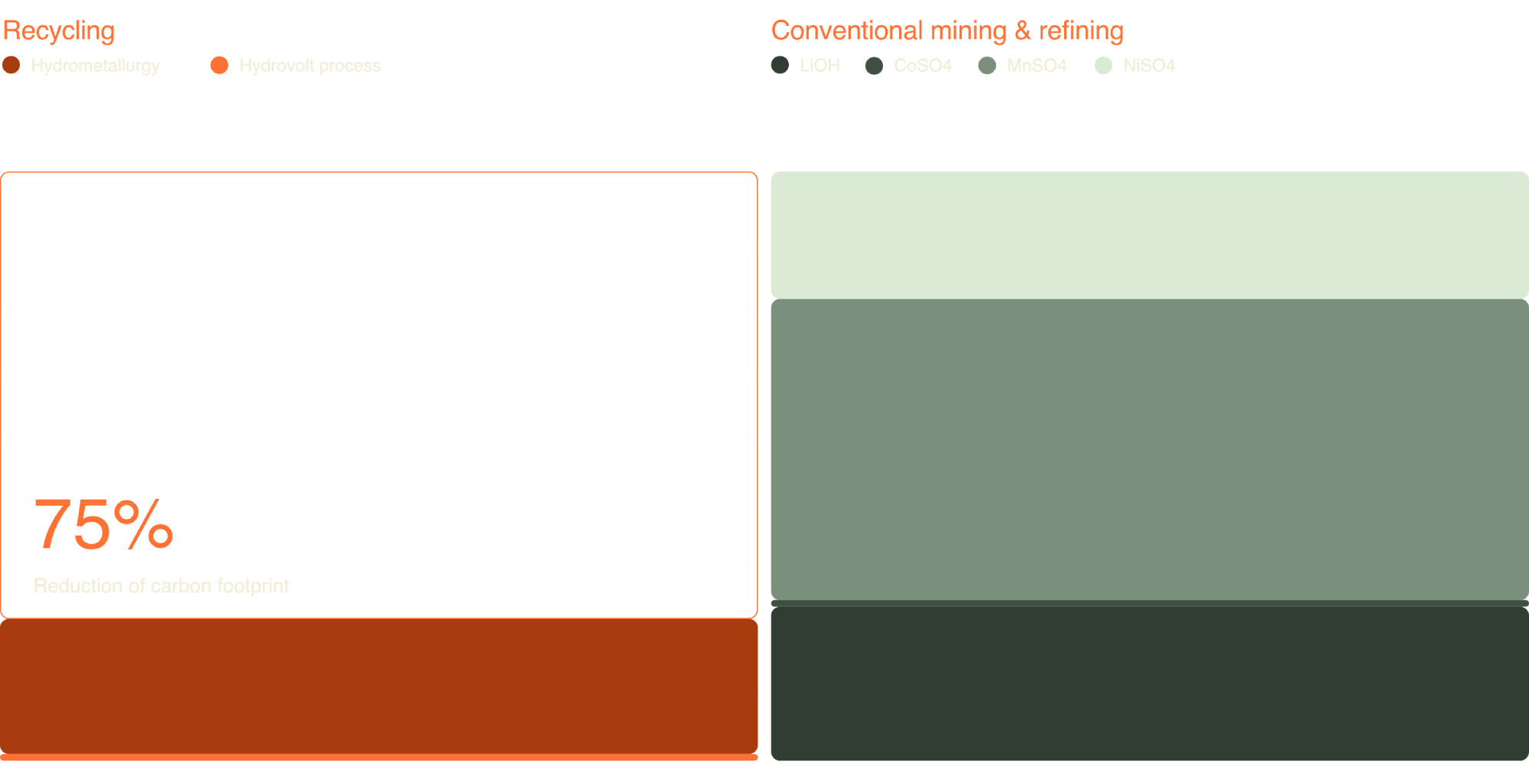
Full transparency
We innovate to ensure full transparency and traceability of the batteries through our recycling process.
Less transportation
We ensure easier logistics and reduced environmental impact as we aim to operate locally.
Market pioneers
Running one of Europe’s largest battery recycling plants since 2022, making us one of the leading actors in the market.
Smaller footprint
Our black mass has 75% lower carbon footprint compared to conventional mining.
100% materials back
We aim for the highest recovery rates in the battery market and work our way up to a 100%.
Safer & cleaner
Our unique automated D&D and dry-environment process offer enhanced safety and cleaner output.